MSc’s high standard of quality extends from research and development to implementation and maintenance. MSc provides service and support for a wide range of industries, extending the life cycle of applications, preventing downtime and maximising availability.
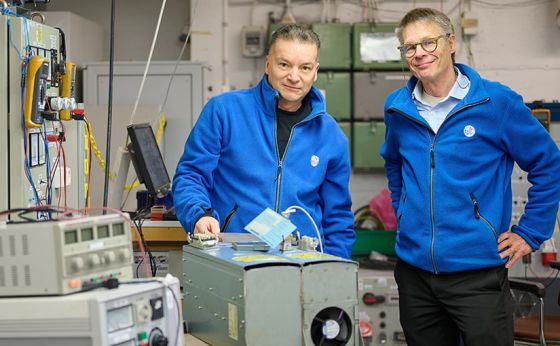
The benefits of proactive maintenance
To ensure that your critical power electronics components deliver consistent performance and reliability, MSc recommends regular preventive maintenance checks and updates. Adhering to a preventive maintenance plan with your trusted service partner can bring the following benefits:
- Long lifespan for your investment
- Optimal performance for your power electronics applications
- Increased reliability of operations
- Minimal downtime and disruption
- Improved safety of operations
- Quick service response time throughout the year
- Enhanced sustainability through longer product life.